In the dynamic world of food processing, efficiency and innovation are key drivers of success. One often overlooked yet crucial component in this industry is the tank coil. These versatile devices have found a myriad of applications in food processing plants, revolutionizing the way we handle, store, and process food products. This article delves into the innovative uses of tank coils in food processing plants, shedding light on their multifaceted roles and benefits.
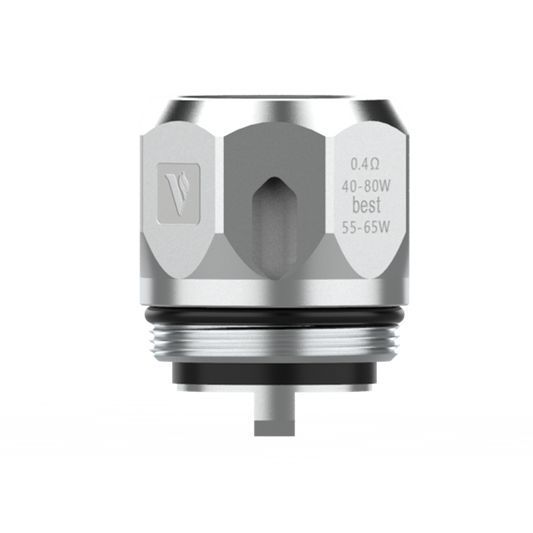
Temperature Control and Stability
One of the primary functions of tank coils in food processing plants is to maintain precise temperature control. Whether it's heating or cooling, tank coils ensure that food products are kept at optimal temperatures throughout the processing stages. For instance, in dairy processing, maintaining the right temperature is crucial to prevent spoilage and ensure product quality. Tank coils facilitate this by circulating hot or cold fluids around the tanks, providing consistent and reliable temperature regulation.
Efficient Heat Exchange
Heat exchange is another critical application of tank coils in food processing plants. By utilizing tank coils, plants can efficiently transfer heat between different mediums, enhancing energy efficiency and reducing operational costs. For example, in brewing, tank coils are used to cool down the wort rapidly after boiling, ensuring that the fermentation process begins at the right temperature. This not only improves the quality of the final product but also speeds up the production process.
Enhanced Mixing and Homogenization
Tank coils also play a significant role in mixing and homogenizing food products. In processes where uniformity is essential, such as in the production of sauces, dressings, and dairy products, tank coils help achieve consistent mixing. By circulating fluids within the tank, they create a uniform temperature distribution, preventing hotspots and ensuring that all ingredients are evenly mixed. This results in a higher quality product with a consistent texture and flavor.
Improved Cleaning and Sanitation
Maintaining hygiene is paramount in food processing plants, and tank coils contribute significantly to this aspect. They are often integrated into cleaning-in-place (CIP) systems, where they help circulate cleaning solutions throughout the tanks. This ensures thorough cleaning and sanitation, reducing the risk of contamination and ensuring compliance with stringent food safety standards. For example, in the production of beverages, tank coils help maintain the cleanliness of storage tanks, preventing microbial growth and ensuring product safety.
Energy Efficiency and Sustainability
In today's environmentally conscious world, energy efficiency and sustainability are crucial considerations for food processing plants. Tank coils contribute to these goals by optimizing energy usage. By efficiently transferring heat and maintaining temperature stability, they reduce the need for excessive energy consumption. This not only lowers operational costs but also minimizes the environmental footprint of the plant. For instance, in the production of frozen foods, tank coils help maintain the required low temperatures with minimal energy expenditure, promoting sustainable practices.
Conclusion
The innovative uses of tank coils in food processing plants are vast and varied. From temperature control and heat exchange to mixing, cleaning, and energy efficiency, these versatile devices play a pivotal role in enhancing the efficiency and quality of food processing operations. By leveraging the capabilities of tank coils, food processing plants can achieve higher productivity, better product quality, and greater sustainability. As the industry continues to evolve, the importance of tank coils in driving innovation and efficiency will only grow, making them an indispensable component of modern food processing plants.